ParAlign Roll Alignment Services from the innovators of inertial alignment.
ParAlign is a unique, non-optical measurement method using inertial technology designed to measure the parallelism of rolls in production installations in the paper, print, converting, steel industries, and web-handling/roll to roll transfer processes.
Misalignment in rolling machinery can lead to wasted material, inconsistent or low-quality products, and excess machine wear. Properly aligned rolls perform better, create more consistent products, and reduce wear and tear on machinery.
Three-ring laser gyroscopes enable the ParAlign to take measurements in three-dimensional space (roll, pitch, and yaw). No line of sight is required, which creates consistent, reproducible results.
Why choose a ParAlign Service?
How can we help you?
Please send us your inquiry and our experts will get back to you shortly
Contact usTraining
We offer alignment, vibration & balancing, ultrasound, and reliability training.
Find a courseTypes of Services
The Pruftechnik Services team offers two types of roll alignment utilizing the ParAlign gyroscopic technology:
the ParAlign Service and the Peak RGA Service.
The ParAlign Service is performed with the ParAlign alone. When performing the service, the device is placed on a roll and swept a minimum of 20 degrees about the roll's circumference. The ParAlign can be positioned anywhere along the circumference of the roll as long as there is enough clearance to complete a proper measurement using the SWEEP method. This flexibility allows for rolls to be measured on the top, bottom, or sides, depending on which is most accessible.The measurement takes about 30 seconds, and results are instantly transmitted wirelessly to a laptop.
The Peak Roll and Geometrical Alignment (RGA) Service is a total alignment solution combining the ParAlign with laser trackers to align rolls and their surrounding structures in the shortest time possible—while producing accurate results and instant visual reports. No other roll alignment method combines gyroscopic and laser tracker technology.
Frequently Asked Questions
Well-aligned rolls—that is, rolls which are parallel to each other—improve product quality and increase productivity through higher machine availability and production output.
The parallelism of rolls is critical when machines run at high speeds or when rolls are in close proximity.
Why should rolls be parallel?
Rolls should be parallel to ensure that the product being created is uniform and of good quality. Parallel rolls reduce or eliminate these issues: uneven bearing stresses, tracking, web breaks, uneven coating, wrinkling, delamination, warping, roller surface wear, tension irregularities, and more. Proper roller alignment minimizes waste, downtime, and maintenance costs.
The parallelism of rolls becomes even more important when machines are running at high speeds or where the web has high contact wrap with rollers.
Why use ParAlign?
It is the fastest roll measurement method on the market.
With a quick setup procedure and measuring process, entire machines can be measured during short maintenance outages. Results are instantaneously displayed, allowing necessary corrections to be made swiftly and adjusted rolls to be re-measured immediately.
The Peak RGA service can even measure rolls in enclosed sections or across multiple machine levels because, unlike optical measurement systems, the ParAlign does not require a line of sight. Also, no baseline is needed for the measurement because the offset is defined in relation to a reference roll.
How does the ParAlign work?
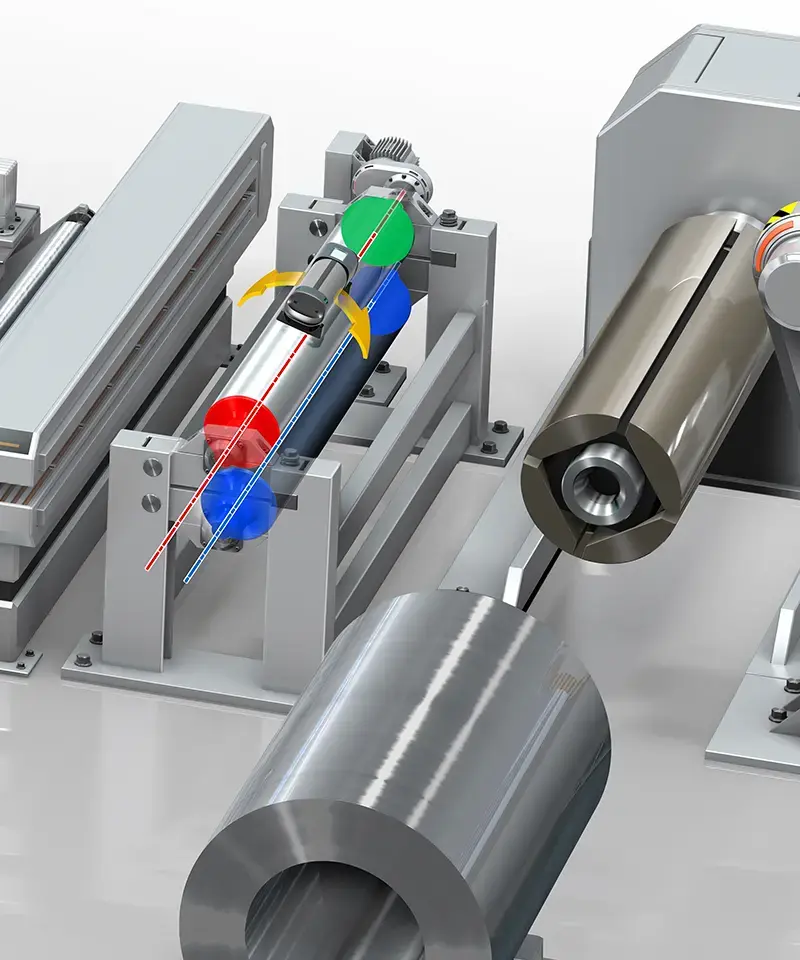
Three ring laser gyroscopes enable the ParAlign to take measurements in three-dimensional space (roll, pitch, and yaw). No line of sight is required, which creates consistent, reproducible results.
In performing a measurement, the device is placed on a roll and swept a minimum of 20 degrees about the roll's circumference. The ParAlign can be positioned anywhere along the circumference of the roll as long as there is enough clearance to complete a proper measurement using the SWEEP method. This flexibility allows for rolls to be measured on the top, bottom, or sides, depending on which is most accessible.
The measurement takes about 30 seconds, and results are instantly transmitted wirelessly to a laptop.
What is the smallest roll the ParAlign can measure?
Does accuracy depend on the location of the roll?
The ParAlign does not drop in accuracy based on location, elevation, or proximity.
How are reports made available?
Is Peak RGA a tool or service?
Peak RGA is a service combining the ParAlign with laser trackers to measure all roller assets in the shortest time possible—while producing accurate results and instant visual reports. No other roll alignment method combines gyroscopic and laser tracker technology.
Do you need optics to set up your measurements?
The ParAlign does not require a visual line of sight to gather alignment data. This means it can measure enclosed oven rolls, tower rolls, or rolls located across multiple floors or levels. However, the software can incorporate optical data from a baseline if required.
What is inertial technology?
Downloads
What our clients say?
Roll alignment with PARALIGN
PARALIGN is the fastest roll measurement method in the market